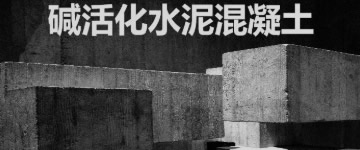
Alkali activated cement concrete
With the improvement of public awareness of the climate crisis and the gradual strong policy and legal intervention of governments in carbon reduction, enterprises are increasingly interested in low-carbon and carbon storage materials. Building construction accounts for more than 11% of global carbon emissions, most of which are generated in the production and processing of building materials. These new materials are likely to transform building materials from major carbon emission sources to negative carbon materials. This type of new materials include: alkali activated cement concrete, soil board, bricks/boards for algae growth and algae derived materials, agricultural waste boards (such as grain straw), special fibers (such as hemp), etc. We are exploring the existing literature to study the above materials. Next, we will verify the durability, structural capacity, humidity, thermal conductivity, fire resistance and other properties of the materials in our own laboratory.
Alkali activated cement concrete is a very important research field at present. Alkali activated cement (AACs) includes a new type of Portland cement substitute formed by alkali activation: a process that uses base or base chemical activator to promote the dissolution of aluminosilicate precursor, and then precipitates to produce cementation reaction. Fly ash, slag and calcined clay can be used as alkali activated cement precursors, among which slag and calcined clay are more sustainable. All kinds of alkali activated cement products, such as mortar, concrete, brick, solid/hollow block, roof tile, insulating concrete, temperature resistant coating and paving brick, have shown equivalent or even better performance than those produced by Portland cement.
Precursors rich in alumina and/or activated silica cannot react directly with water, they need an activator to cure and harden. Common alkali activators include caustic alkali, silicate and weak acid silicate. In the slag activation process, the reaction starts from the attack of alkali on slag particles. As the outer layer is destroyed, it continues to polymerize as a reaction product, forming the initial product through dissolution and precipitation. In the later stage, the solid mechanism is followed. As the ions slowly diffuse to the unreacted core, the later reaction occurs on the surface of the formed particles. In the initial stage of hydration, the exchange of alkali metal cations (R+) and calcium ions (Ca2+) shows a pure catalytic effect. The equation is as follows:
Hydration products after slag activation are similar to those of traditional Portland cement, but the Ca/Si ratio is relatively low.
According to research, GGBFS (finely ground granulated blast furnace slag) is the most effective cement substitute material in concrete manufacturing, which is mainly composed of CaO/SiO2/Al2O3/MgO and some other trace oxides. The hydration behavior of GGBFS can be quantified by alkalinity coefficient (Kb):
The equation can be simplified by excluding the equal important components (usually less than 1%):
According to the alkalinity coefficient, GGBFS can be divided into three groups: acidic (Kb<0.9), neutral (Kb=0.9~1.1) and alkaline (Kb>1.1). Neutral and alkaline materials are more suitable as precursor materials.
The fineness of slag, the property and modulus of activator (mass ratio of SiO2 and Na2O or K2O) and curing temperature will have an important impact on the mechanical properties of mortar. In fact, according to existing research, compared with traditional Portland cement concrete, the mechanical properties and durability (including chlorine resistance, acid resistance, etc.) of alkali activated cement concrete can reach acceptable standards by adjusting various influencing factors. For activator, it is generally recommended to use the best modulus of 1.0-1.25 in the mixture to obtain better strength and durability. There is no relevant standard for the proportion of aggregate and binder, and the proportion of coarse aggregate and fine aggregate. The mixing proportion is generally obtained through repeated tests to meet the specified requirements.
When using traditional aggregate, alkali activated cement concrete shows better chemical resistance than Portland cement concrete. In addition, alkali activated cement concrete shows better performance in terms of high temperature resistance and freeze-thaw resistance. In the aspect of reinforced concrete, alkali activated cement concrete shows the same performance as Portland cement concrete under load, sometimes better.
However, there are still many aspects of alkali activated cement concrete that need to be studied in depth, such as: fluid properties, high-strength and ultra-high strength concrete (100-120Mpa and above)